
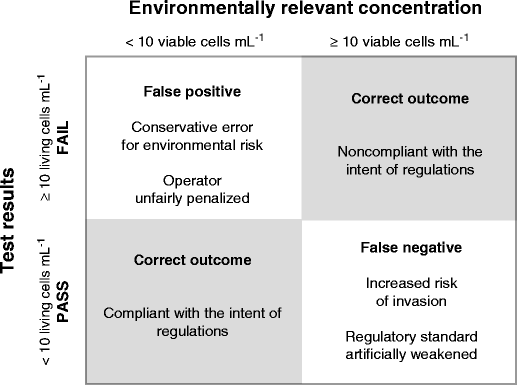
The precision in all cases generally worsened as the serial dilution proceeded across the plate this was expected as the error in the earlier columns propagated with each transfer. Three mixes before each transfer yielded an average CV of 11.8%, while 20 mixes gave a considerably better CV of 1.7%. The average precision (averaging CVs for columns 1–10) improved asymptotically as the number of mix cycles increased.
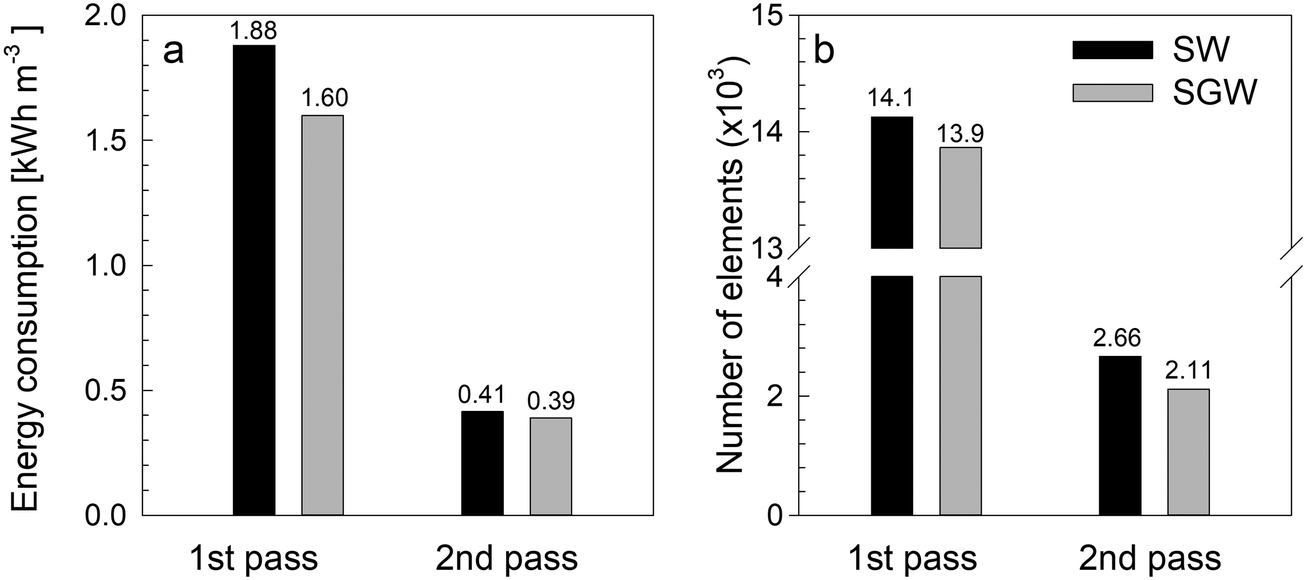
The first experiment varied the number of mixing cycles between 3 and 20. A calibration curve was prepared, and each experimental dilution concentration was plotted against the standard curve to determine the real concentrations in each column. The second indication was the accuracy of the transfer. The CV also provided information on the propagation of error across a plate-the CV increased sharply across the plate if mixing was incomplete. The Coefficient of Variance (CV) of each column indicated the precision of the mixing step. Two measures were used to evaluate mixing efficiency. Transfers were previously determined to have a precision and accuracy of >99% at this volume any observed deviations in precision and accuracy were due to error propagation from ineffective mixing. There are two main components of an accurate and precise serial dilution: the accuracy and precision of the transfer and the efficiency of mixing. The starting volume was 300 µL, and 200 µL tips were utilized for the transfer (150 µL, a 1:2 dilution) and mixing steps (190 µL). The basic experiment diluted fluorescein across the columns of a 96-well plate, from A1 to A10 (A11 and A12 were blank wells). The goals were to determine which parameters had the greatest effect on mixing and to reduce the time required to perform a serial dilution. With the platform’s VWorks™ software, the application allowed the total control of liquid transfer and mixing heights and speeds, which allowed efficient exploration of mixing parameters.
#IMPORTANCE OF SERIAL DILUTION IN DESALINATION PLANTS FULL#
Velocity11’s (Bravo™ Liquid Handling Platform performed serial dilution with the same pipette head as a full plate dispenser (Figure 1). To overcome these challenges, the effects of various mixing parameters of a serial dilution protocol were explored. These challenges greatly limit the throughput capacity of an automated serial dilution system. To compensate for this error possibility, longer mixing times are required, which then increases the time required to perform the serial dilution. The result is that the highest dilutions will have the most inaccurate results. With each sequential serial dilution step, transfer inaccuracies lead to less accurate and less precise dispensing. The first is error propagation across columns or rows. Serial dilution processes face two major challenges.
